Problem statement
Improper hole cleaning is a major cause of non-productive time (NPT) in drilling. Current hole cleaning practices are mostly based on experience, rules of thumb and simplistic calculations, and do not necessarily work as expected in all scenarios. Available models do not include parameters such as fluid compressibility, pipe rotation and eccentricity, and transient effects. They often do not work with state-of-the-art technologies. These modeling software are also extremely expensive. There is a need for a robust, fast, cost-effective and accurate tool to simulate cuttings transport, and provide reliable and useful estimations of hole conditions in real-time.
Technology description
Over several years, researchers at The University of Texas at Austin have used experimental and field data to develop a model (RAPIDClean) that simulates transient multiphase flow of liquid and solid particles (cuttings) inside wellbores during drilling and hole cleaning operations (DOI: 10.2118/201461-MS). It can provide invaluable information regarding the required drilling parameters for optimum hole cleaning and avoid further issues such as stuck pipe. Moreover, the status of the cuttings bed can be monitored in real-time and necessary cleanup cycles can be performed to avoid excessive pressures and torques in the well. The numerical scheme used, allows for simulations that are several times faster than the real-time operations, providing the crew with enough time to take preventive actions. This software can run on a standard desktop PC and can integrate with a larger suite of software (RAPIDKick), developed and maintained by the same researchers, to provide a single wellbore multi-phase flow simulator for the latest drilling technology. MPD operations can also be simulated using the model.
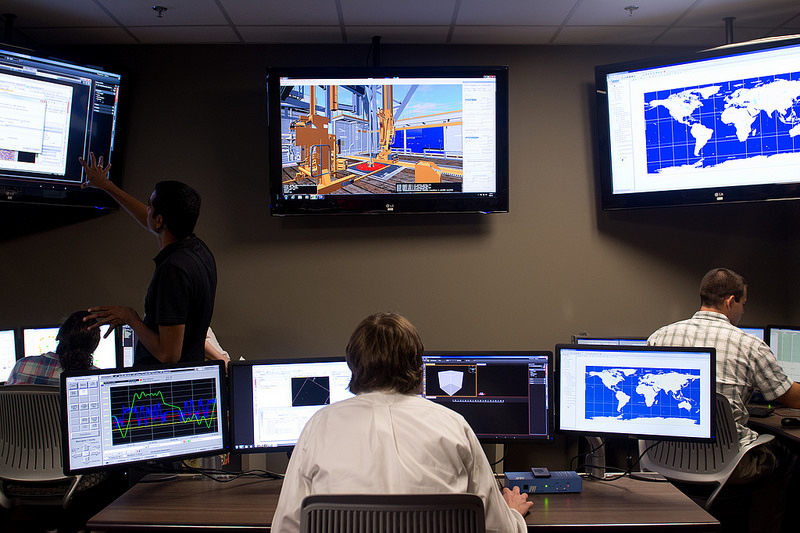
Stage of development
Software (alpha). Case studies were performed based on field experiments to analyze the effectiveness of the developed model on avoiding operational problems such as pack-off and stuck pipe. Results show that by monitoring the real-time cuttings concentration and bed height along the wellbore, the developed model can detect improper hole cleaning conditions and provide optimum drilling parameters to resolve problems, thereby minimizing NPT. We are currently looking for commercial partners to evaluate the product in the field.