Problem statement
Hydraulic fracturing involves fracturing of bedrock formations by pressurized liquids and is one of the key technologies used for unconventional oil production. Usually strains on the order of 10–5 to 10–6 propagate ahead of the fractures. Monitoring and characterizing the strain on wellbores can be a formidable challenge, especially in pre-existing wells that cannot be retrofitted with sensors.
Currently used sensors for horizontal wells are basically long fiber-optic cables that stretch when the casing pipe elongates under strain load from the surrounding matrix. These devices give overall strain over their length but are not good at pinpointing local events. The pipe wall has a nominally circular cross-section, but external force will deform this cross-section elliptically. Since we can’t mount strain gauges onto existing pipe below ground, an indirect method of measuring changes in strain is required that is capable for determining local strain.
Technology description
Researchers at The University of Texas at Austin have come up with a novel and effective way to measure strain in a wellbores, primarily to diagnose the geometry of hydraulic fractures in the subsurface. It takes advantage of the presence of centralizer bow-string assemblies already used in oil-well tools. These centralizer spring units deform to position downhole oil-well tools in the center of the casing and provide clearance as the downhole tools transition across joints and bends during insertion and removal. By mounting strain gauges in specific locations on the bow-spring assembly we can monitor changes in the strain induced in the casing that is in contact with the centralizer spring assembly (Fig. 1).
Ambient mechanical pressure at depth pushes the matrix rock (like shale), cement, and casing pipe together firmly enough that slipping between the interfaces cannot occur. Therefore, the casing pipe will be strain matched to the surrounding rock matrix. Specifically, the strain measured inside of the pipe will be the same as the strain induced in the surrounding rock. The strain measurements can be made at multiple locations in the well and the assembly of strain sensors can be moved to different locations in the well as the fractures are created in the adjacent well. This allows the measurements to be made across a long length of wellbore with a limited number of strain sensors. The measurements can then be interpreted using a geomechanical model to infer the fracture length, width, and orientation.
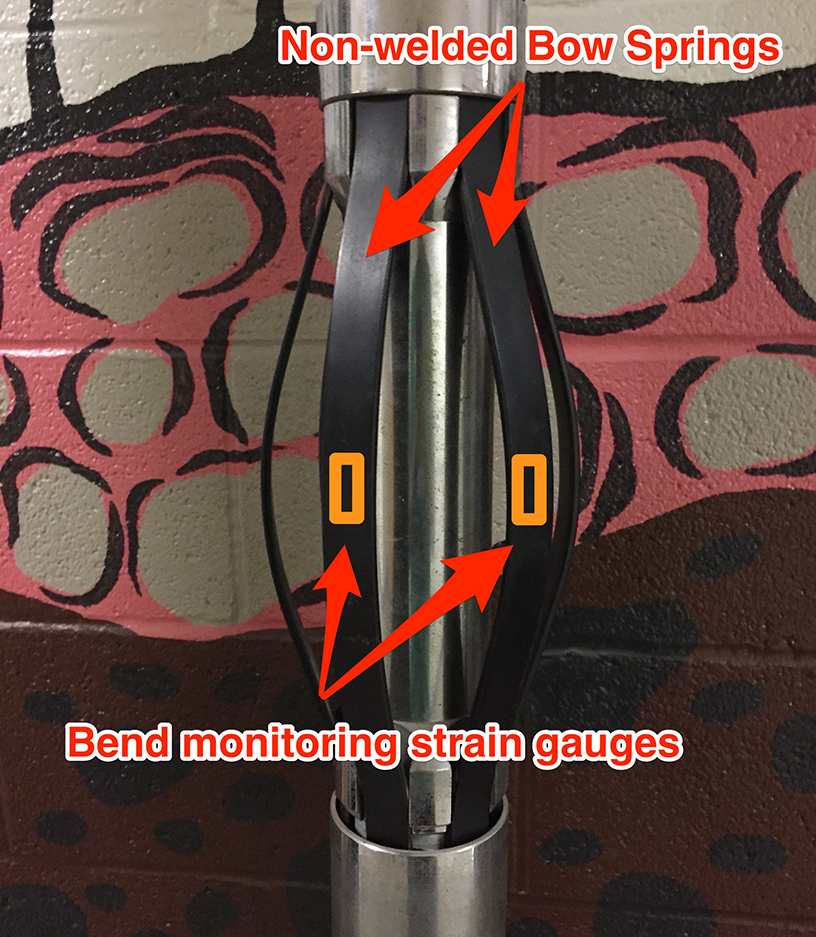
Fig. 1: Sensor placement
Benefits
- Inexpensive and easy to install
- Operator can choose the location and number of sensors.
- Can be retrofitted into existing wells
- Same set of sensors can be moved in the wellbore to record the data from the entire length of wellbore.
Stage of development
The University of Texas is looking for commercial partners and investors to build and test this tool in the field. IP Position: Published PCT application, nationalized in US ( WO2019232521A1)